With so many different glove coatings on the market, it can be confusing what type of work glove coating will work best for your particular application or job. Glove coatings are an important feature on any glove because it helps to enhance the grip and protection you receive while wearing the glove. Here we try to shed some light in an effort to help you choose the correct glove coating for your job!
Nitrile
A nitrile coated glove is a very popular synthetic alternative to latex and is perfectly suited for many industries including metal fabrication, assembly, and automotive factories. The main strengths you’ll find from a nitrile coating are that it has an extremely high abrasion resistance and its peak performance temperatures are between -25° F and 300° F. The weakness that you’ll find with nitrile is that it doesn’t have the best grip in wet and oily conditions.
Foam Nitrile
A foam nitrile coating is achieved by putting regular nitrile through a process of mechanical mixing which creates this foam coating that acts like sponge. This allows liquid to be soaked up, maintaining a good grip. Foam nitrile coating is suited for many industries, including automotive, small parts handling, and construction. The three main advantages to foam nitrile is that it offers superb grip in both wet and oily environments, the coating has a moderate level of abrasion resistance, and it has great dexterity and breathability. The two disadvantages to foam nitrile is that this coating doesn’t do very well with adhesive products and any liquids you handle while wearing these gloves will penetrate the coating, as that is what the foam nitrile is designed to do.
Micropore Nitrile
A micropore nitrile coating is created when nitrile goes through a process that infuses it with millions of tiny bubbles. These microscopic bubbles significantly increase the grip of the glove because the bubbles create tiny suction cups which displace the liquid they come in contact with. These gloves are perfect for any industry that requires strong grip, like metal fabrication, manufacturing, and automotive. The main strengths of micropore nitrile are their extremely good grip in oily and wet environments, their high level of abrasion resistance, and compared to the foam nitrile, they have a lower soak through rate for liquids. Despite there overall great grip, the one area they are week is with their grip in adhesives.
Neoprene
This coating is made from neoprene, a synthetic rubber manufactured by the polymerization of chloroprene. This coating has a high level of chemical stability and heat resistant properties, which means it is the best choice for any industry or application that requires chemical or fire resistance. The main advantages of neoprene coating is its excellent grip in all conditions: dry, oily, or wet, it is resistant to oil and is also fire and flame resistant. The main weakness of this coating is that is has a very low abrasion resistance.
Polyurethane
A polyurethane coating is one of the most popular glove coatings on the market because of its economic value, it allows wearers to maintain dexterity, and it has a low-particulate shed. Polyurethane is a perfect coating for industries such as inspection, detailed assembly and aerospace. The top strengths of this coating are its extreme comfort, superb grip in dry conditions, and its lightweight flexibility. The two disadvantages with this type of coating are its low level of puncture resistance and it does not have good grip ability in wet or oily environments.
Latex
This natural rubber coating works really well for industries that require high levels of grip and durability, including construction, masonry, and landscaping. The top two strengths of latex coating are that it is soft and flexible, which translates to comfort and dexterity and it also offers great grip in dry conditions. The weaknesses found with latex coating are that it is heat sensitive, not very resistant to oils, it has low levels of abrasion resistance, and of course it has the potential to cause allergic reactions.
PVC
PVC, which is short for polyvinyl chloride, is a widely used synthetic coating that is suited for industries like wood working, furniture making, and the petrochemical industry. A PVC coating is your best option for working with adhesives. Some other strengths to this coating are that it has great levels of abrasion resistance, and does very well in cold weather. The downside to PVC is that it has a low level of puncture resistance.
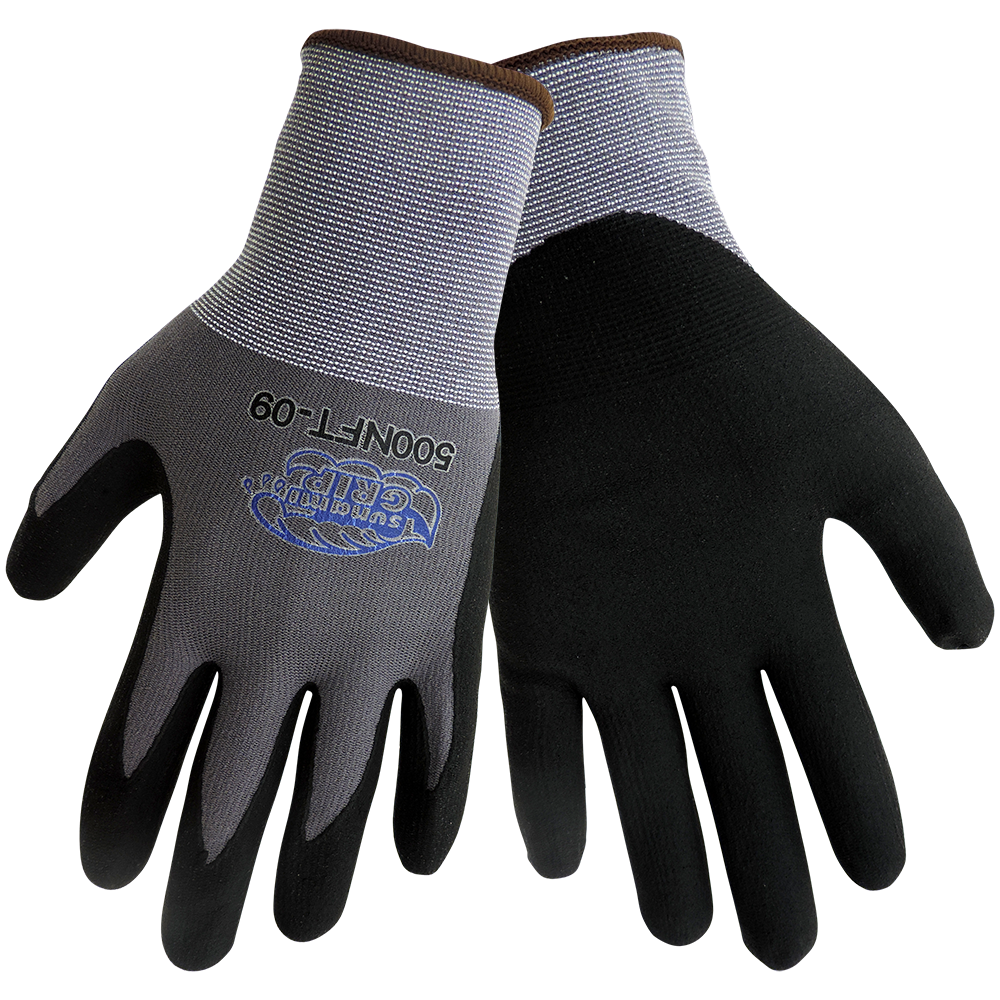